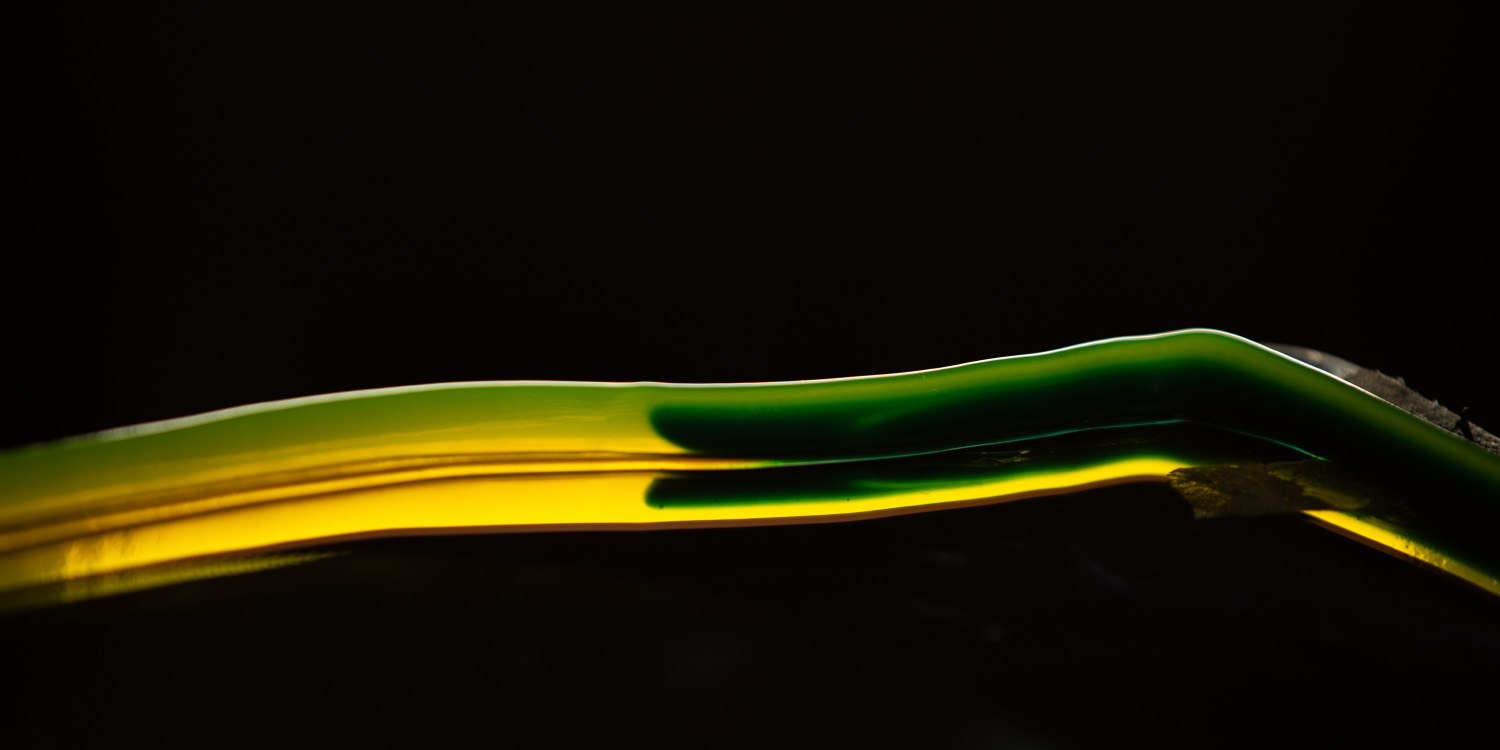
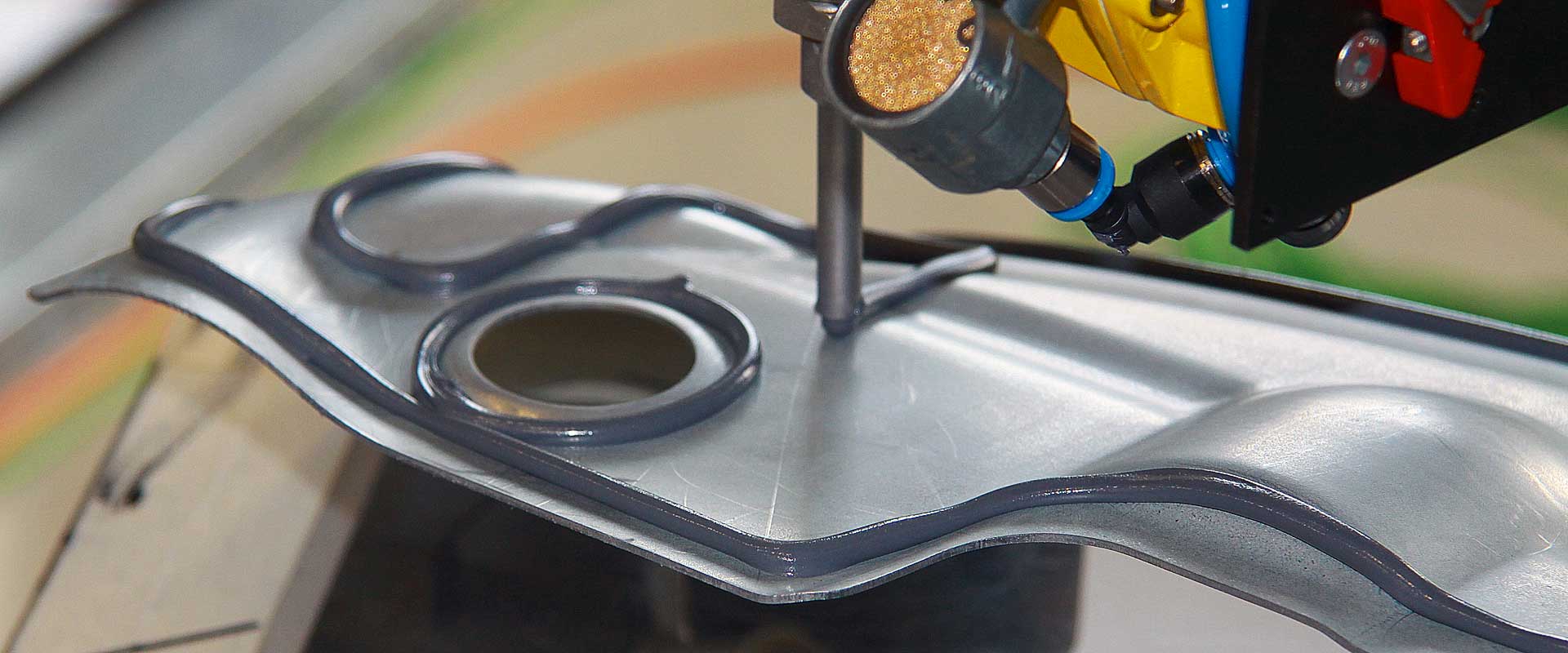
Glue application
Bonding is playing an increasingly important role in engineering. The technology is constantly evolving and is gaining popularity in more and more fields as well as replacing traditional joining methods to boost product quality and open up new areas of application.
ATN is a leader in industrial glue application systems. Our cost-efficient quality products are the result of many years' experience, ongoing development and close cooperation with our customers.
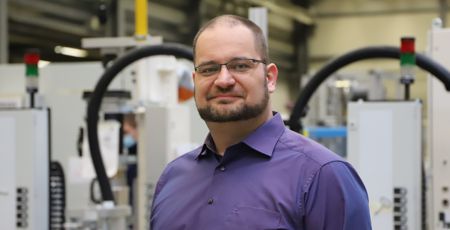
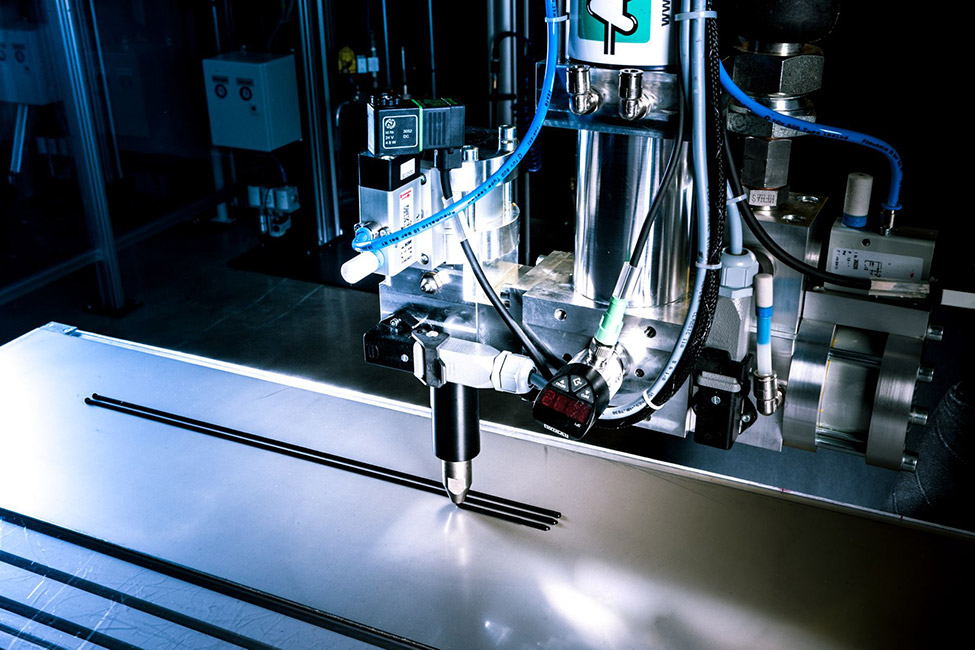
Industrial Glue application systems
ATN application systems accommodate virtually any flowable material in a host of different industrial gluing processes. Our experts will choose from a range of individual components that can be customized to your material properties, process requirements and specifications.
ATN also has specialist expertise in automated glue application. With over 20 years’ experience in plant engineering and automation, we can develop a tailored automation solution for your glue application process.
ATN presents new application technology in trade journal
It is possible with the new adhesive technology of the multi-material-applicator-series to apply two or more different adhesives from one nozzle.
The 10/2023 issue of the trade journal adhäsion KLEBEN + DICHTEN presents the innovative bonding technology of ATN's multi-material-applicator series.
The various advantages and possible applications of the new bonding technology are summarizes in the blog post.
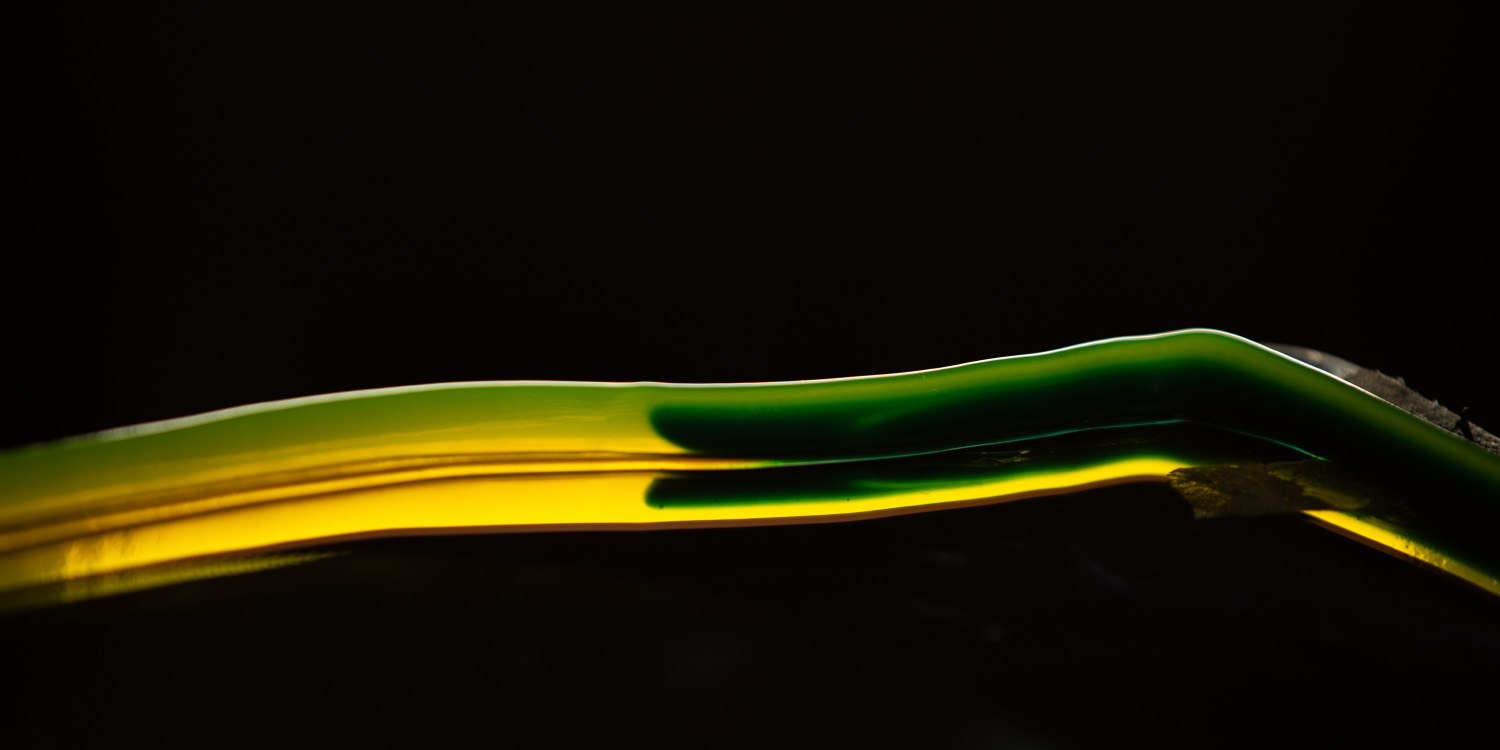
The chemical perspective on glues
Chemically speaking, glues are plastics. Once set, they become thermoplastics, elastomers or duromers (also called thermosets). Glues essentially fall into two categories based on how they create a bond: physically or chemically.
The substances in glues that create a physical bond do not change during the bonding process; they harden via physical processes – often by cooling or solvent evaporation. This category includes hot adhesives (hot melts) and contact adhesives (e.g. tape).
The substances in glues that create a chemical bond do change during the process. This chemical reaction is triggered by a second glue component or by an environmental influence such as humidity. Here it’s crucial to suppress the reaction until the glue is in the joint, which is why two-component glues are not mixed until just before application. One-component glues must be protected from the external influence that activates them.
Getting industrial bonding right
To create the ideal conditions for adhesion between the workpiece and the glue, it is essential to pretreat the workpiece surface, for example by cleaning, priming and activation. The only way to obtain reproducible, high-quality bonds is to ensure that adherend (workpiece) surfaces are even and clean.
To ensure that every workpiece is optimized for gluing, we have developed special surface treatment equipment.
Industrial glue application process designs can be fully automatic, semi-automatic or manual. Whether a particular semi- or fully automatic application process would be more practical and cost-effective using robot-guided application, or via stationary application to robot-guided workpieces, is a decision based on specific process requirements such as workpiece size, available space and cycle time.
Requirements for the perfect industrial gluing system:
The characteristics of the joining materials and the quality requirements of the glued connection determine the shape in which the glue is applied – for example round beads, profile beads, or material application on large surfaces. Our wide range of applicators and compatible application nozzles makes it easy to produce high-grade glue beads in any of these formats.
As well as the bead type, the number of components in the glue will also affect how it is processed, and multi-component glues prevented from mixing before application. Two-component glues cure when their components react together.
A second, booster component can be added to one-component glues to speed up curing and so deliver bonded workpieces more quickly to downstream production processes. Our dosing and application systems can also be extended to two-component versions.
Choosing the right system is the key to high-quality bonds
Gluing systems are used in all kinds of application areas and often require equipment tailored to the process concerned. Our specialists benefit from years of experience in industrial bonding and have implemented many of these customized plants. They will be happy to help you choose the best option for your needs.
See our product overview and product brochure for an initial comprehensive overview of our components. We supply a wide range of standard components, but we can also customize them to suit your specific process.
Our online configurator lets you configure the gluing system you require so that you can get some idea of your system. Based on information about your glue application process, our experts design your system in line with your requirements.
Implement your application process with ATN
ATN’s reliable application systems comprise all the components you need for application across all orders. They include barrel emptying systems, dosing systems, application towers and nozzle cleaning systems as well as many accessories. ATN is your partner for reliable precision fluid dosing systems. ATN application systems guarantee a consistent quality of your processes.
End-to-end application and automation solutions
Looking for an end-to-end solution for your special-purpose machine or system? Get in touch – we’ll be happy to provide you with comprehensive advice on all aspects of application, assembly and automation solutions. We will fully implement your entire process, from conceptual design to on-site commissioning. We offer industry solutions for the automotive, household appliances, aerospace, electronics, renewable energies, chemical, construction and furniture industries as well as medical technology and pharma life science.