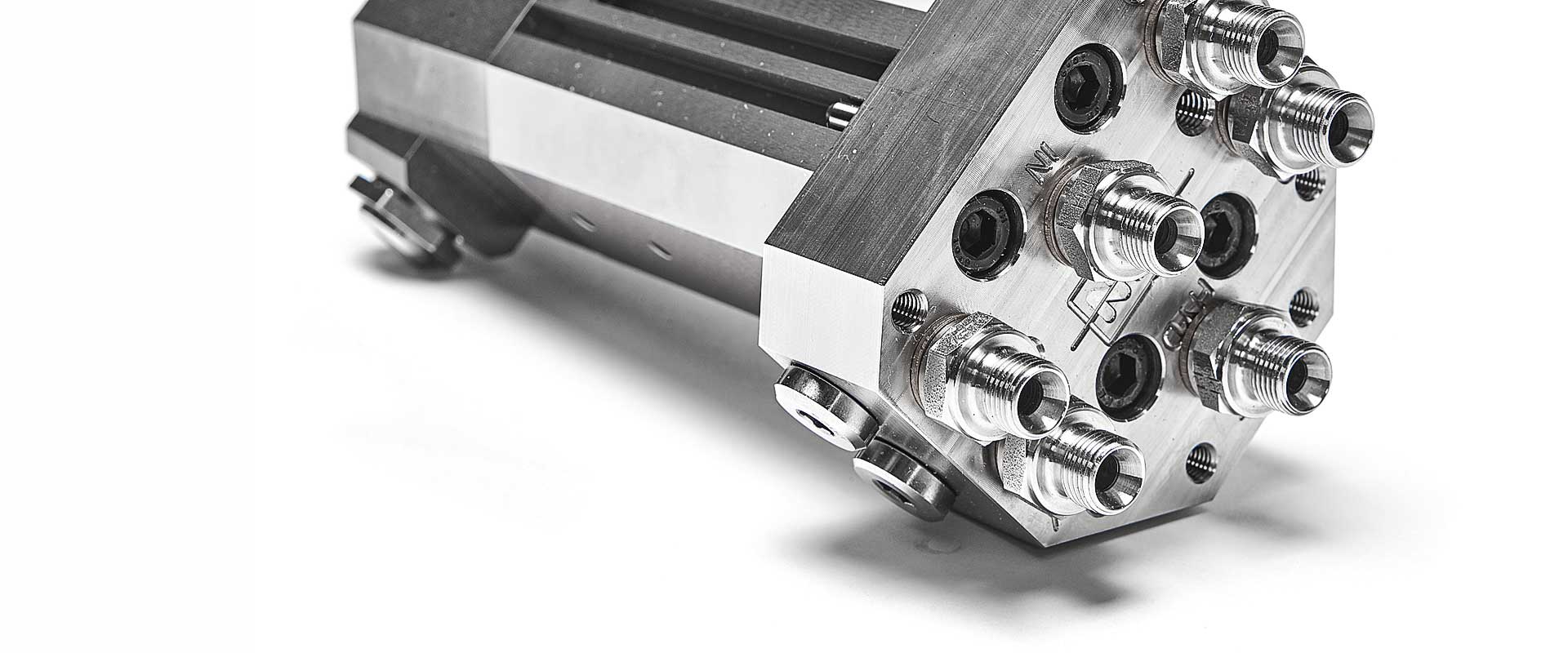
RIM systems
Reactin Injection Moulding (RIM), which uses a chemical reaction to produce PUR foam from two components, requires special technology.
We've acquired years of experience and process knowledge in RIM technology based on ATN RIM systems used in the automotive industry.
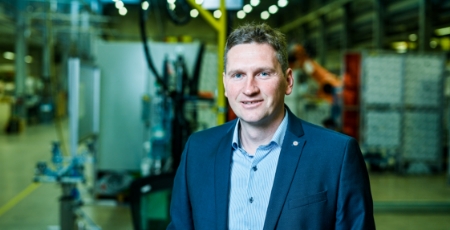
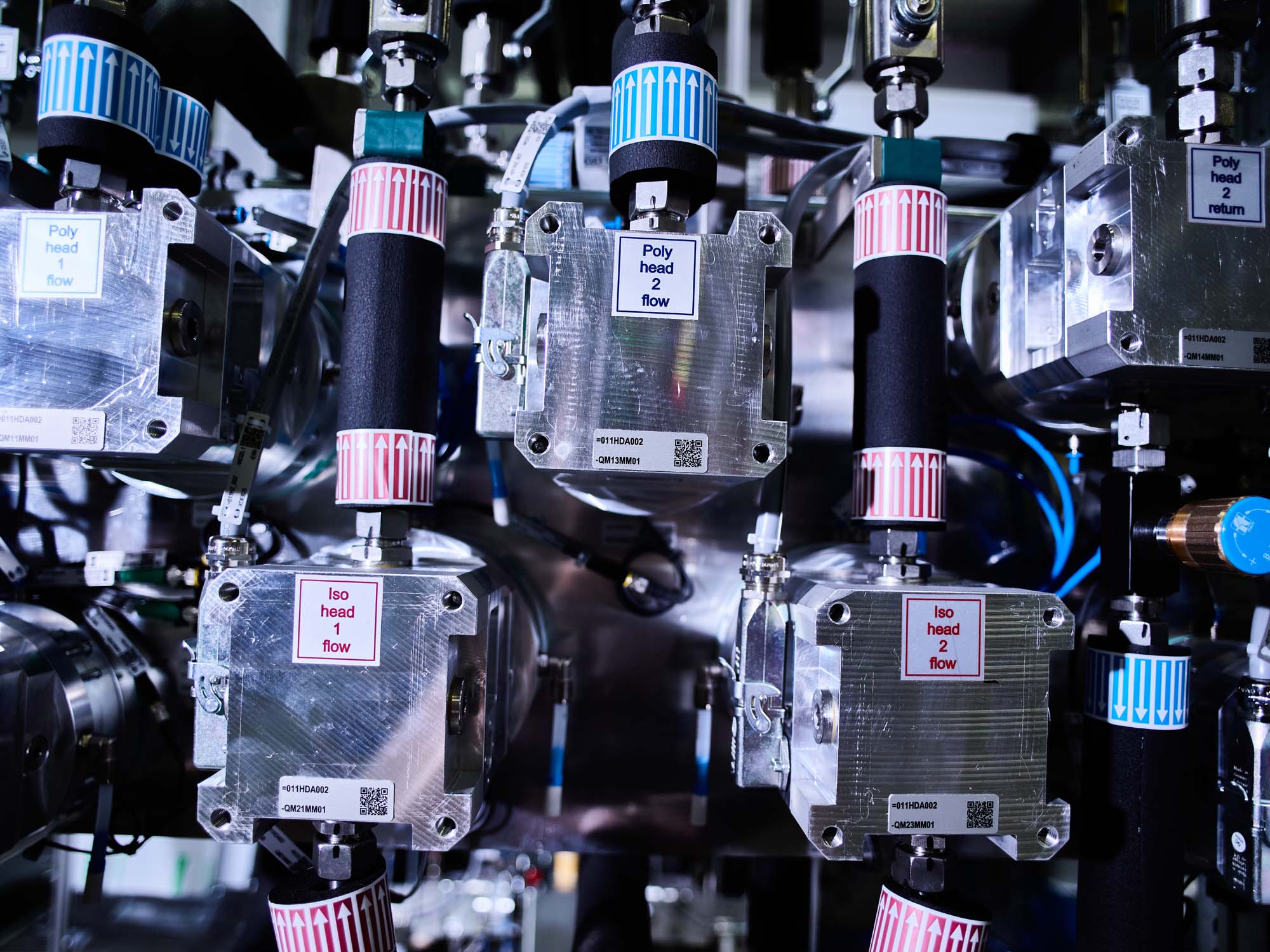
ATN RIM systems with electronic volumetric dosing systems
Combining our two-component RIM application system with ATN dosing systems is a totally fresh approach to processing PUR foams compared with other systems on the market. This proven technology combines maximum dosing accuracy at all material quantities with stable, requirements-based material dispensing. As the system keeps the material moving at the right conditions for application to ensure its availability at all times, there are no material downtimes regardless of ongoing application.
ATN RIM systems deliver high-precision dosing at even the lowest shot volume, and long-lasting service with abrasive and filled materials.
Design and function of the RIM dosing units
Electrically driven volumetric dosing units offer the best control and dispensing properties for the raw materials used. They require no other components or units and are easy to maintain since they are designed with two separate parts – the material feed and the drive.
The dosing unit supplies the applicator with a continuous flow of conditioned raw materials (with isocyanate and polyol for PUR application). During application, dosing unit pressure reaches up to 200 bar and precisely delivers the required material quantities. The streamlined design of our dosing units allows you to position them immediately next to the application point.
ATN volumetric dosing systems for RIM application
Dosing unit | Material quantity | 2C material shot discharge capacity |
---|---|---|
EVD 350 | 10 – 450 ccm | max. 190 ccm/s |
Other dosing unit sizes are available on request.
Design and function of the RIM applicator
The RIM applicator is based on the impingement mixing principle where mixing occurs as the result of a turbulent flow. During the material shot, nozzles (with a cross-section of 0.2 to 1.0 mm) feed the components to a relatively small mixing chamber. Consequently, the component flows collide at high speeds of up to 350 m/s, resulting in a homogeneous mixture.
The applicator is continuously purged when not in use. For automated application, the applicator is flange-mounted on a robot or manipulator.
Manual RIM handling applicator
You can also use the RIM applicator manually with a hand grip and operating point or just a hand grip. The operating point stores up to 10,000 mixing recipes which you can then select as required.
Implement your application process with ATN
ATN’s reliable application systems comprise all the components you need for application across all orders. They include barrel emptying systems, dosing systems, application towers and nozzle cleaning systems as well as many accessories. ATN is your partner for reliable precision fluid dosing systems. ATN application systems guarantee a consistent quality of your processes.
End-to-end application and automation solutions
Looking for an end-to-end solution for your special-purpose machine or system? Get in touch – we’ll be happy to provide you with comprehensive advice on all aspects of application, assembly and automation solutions. We will fully implement your entire process, from conceptual design to on-site commissioning. We offer industry solutions for the automotive, household appliances, aerospace, electronics, renewable energies, chemical, construction and furniture industries as well as medical technology and pharma life science.