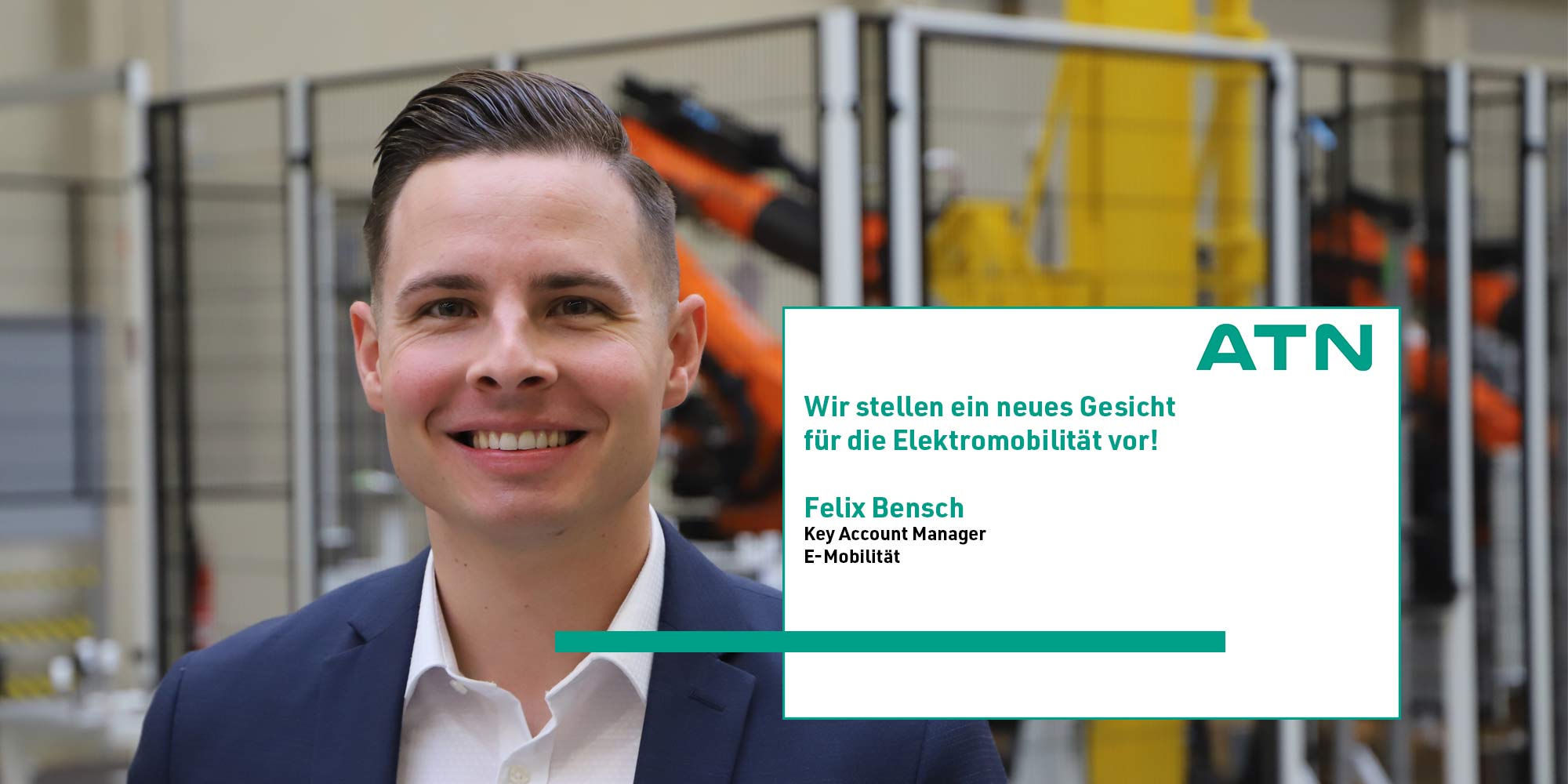
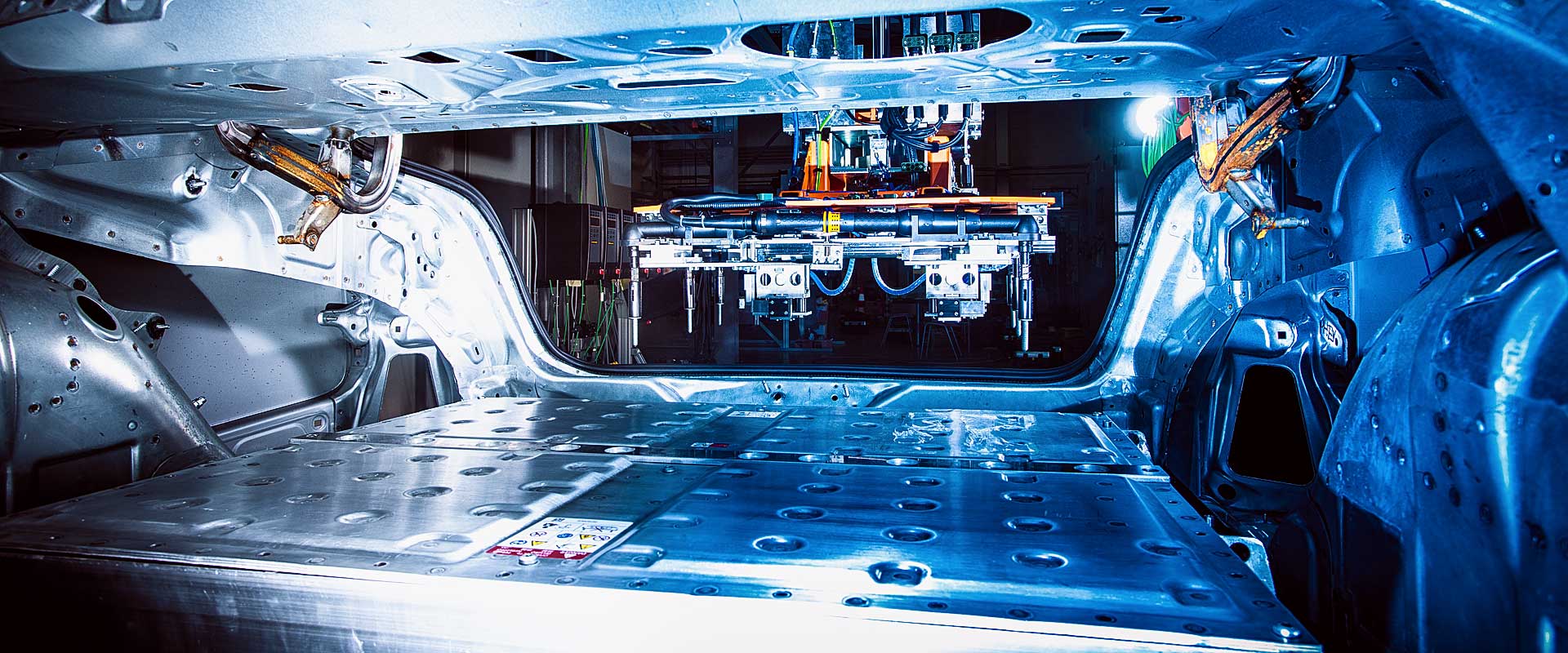
E-mobility: the drive technology of the future
The automotive industry is going through unprecedented changes. Hybrid and all-electric drives are gradually replacing the combustion engine. Car manufacturers are confidently announcing that combustion technology will be consigned to history within a specific time frame. E-mobility is the future of the industry.
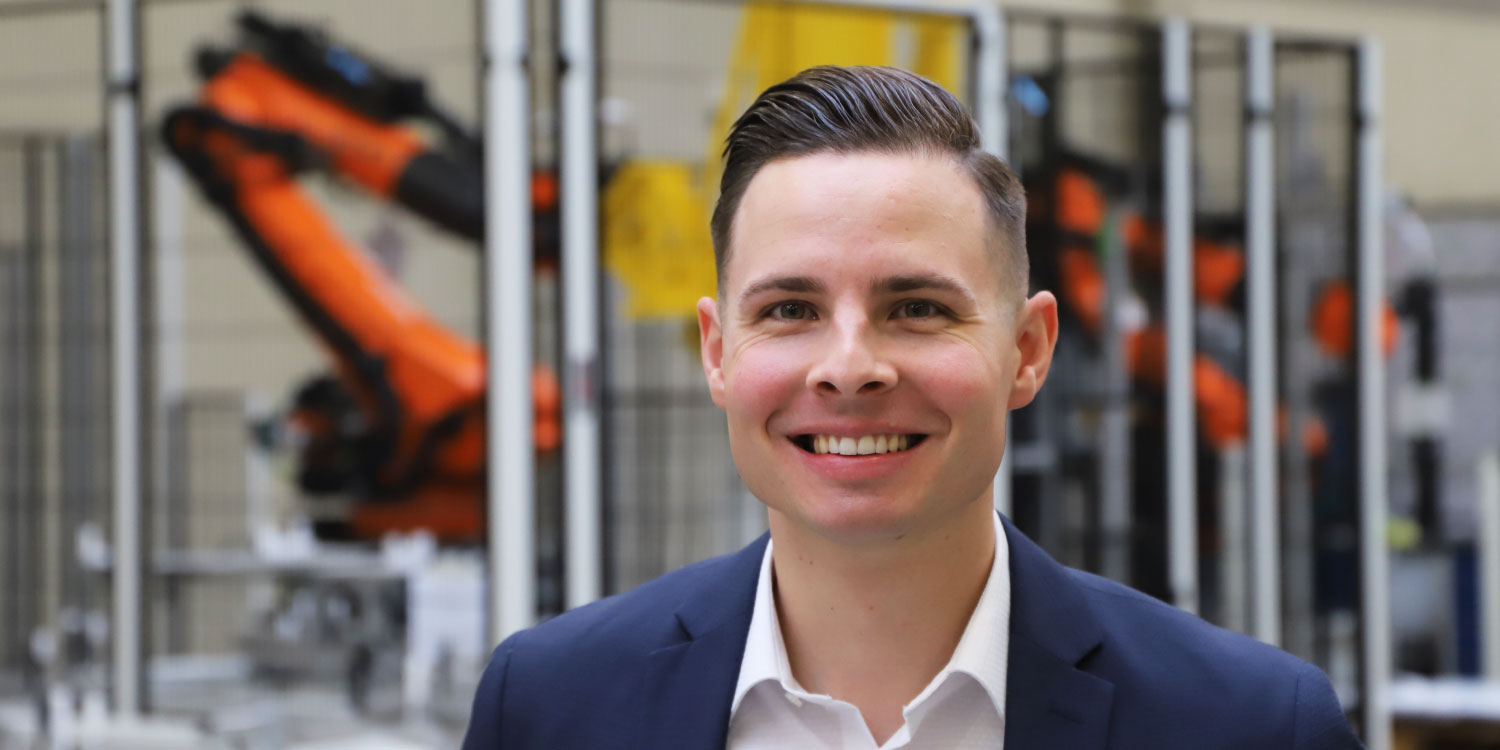
BATTERIES: THE CORE COMPONENT OF E-MOBILITY
Without batteries, there would be no e-mobility. They are maturing at a dizzying pace along with e-mobility in general. Battery ranges and hence mileage potential are increasing while the overall weight of electric vehicles is reducing. Consequently, e-mobility is ever more appealing.
But these changes in drive technology present new production challenges. Long battery service life, performance and safety – and therefore the overall efficiency of e-mobility – come with demanding manufacturing requirements.
New Key-Account Manager E-Mobility
ATN bietet Ihnen ein umfangreiches Leistungsportfolio in der Batteriemontage
Application Technology for E-Mobility
ATN is a long-standing supplier of application and automation solutions for the automotive industry. Our technical specialization and many years of experience also make us a reliable partner in the specialist field of e-mobility production. Our engineering consulting experts have been providing customers with innovative application systems and automation solutions ever since hybrid and electric drives first emerged.
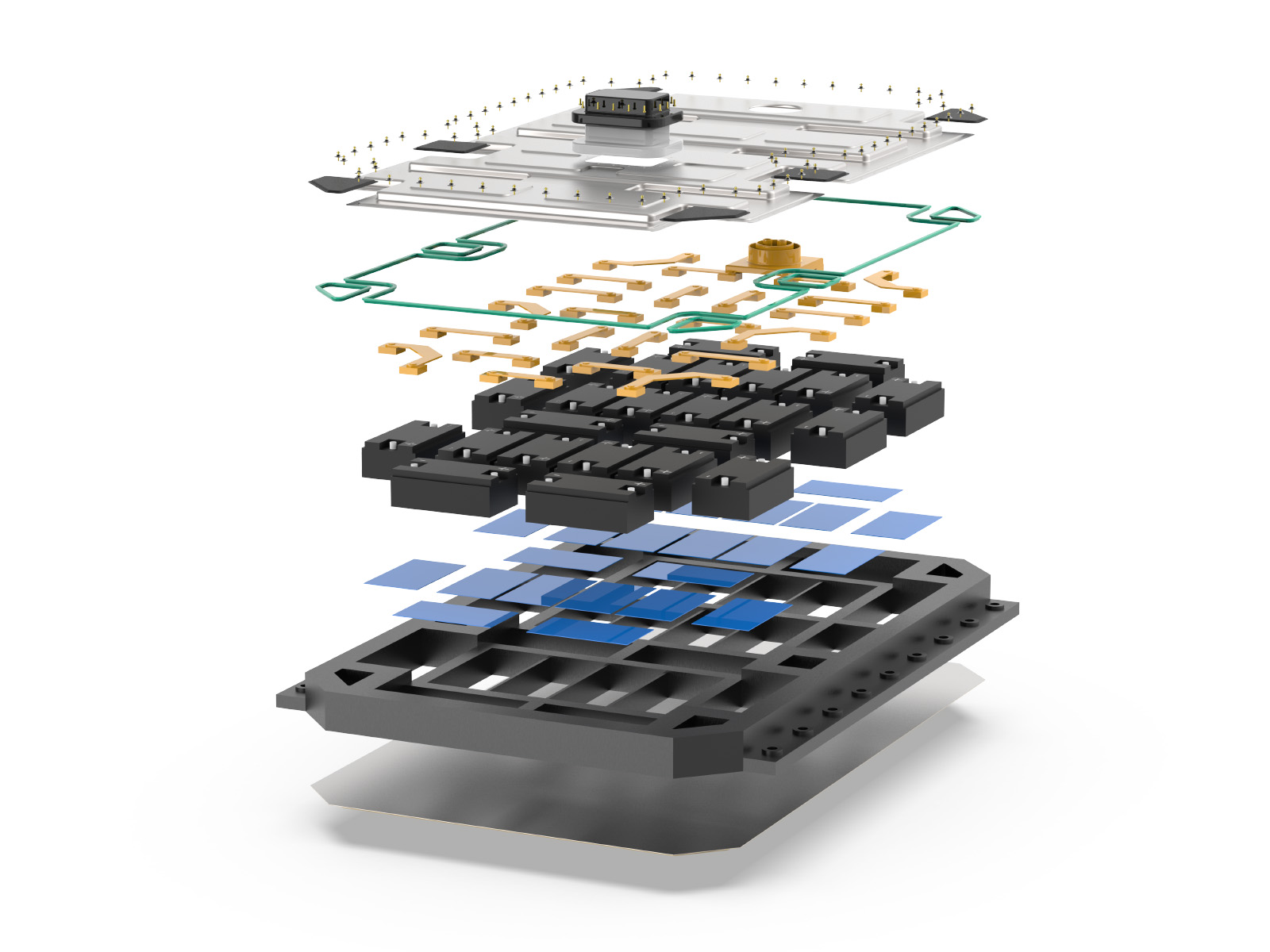
Our applications and processes for battery production and assembly:
As an end-to-end solution provider for battery production, our wide range of application systems can be implemented in high-quality gluing, filling and sealing applications that meet your materials requirements. And courtesy of our technology centre we can also develop customer-specific requirements from pilot to production.
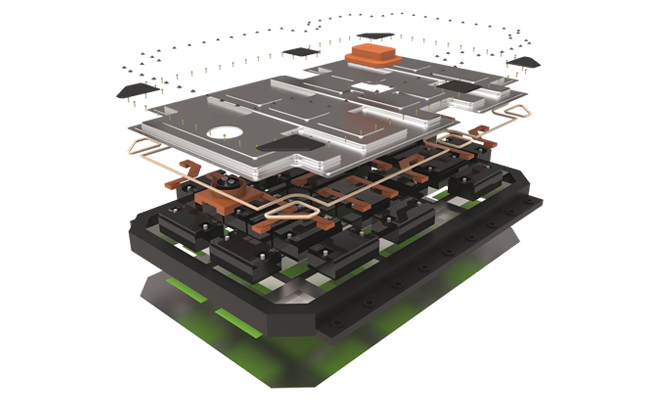
Sequence:
- Component cleaning with compressed air, cloth, or alcohol-based cleaning fluids
- Bonding-surface pretreatment with activating, priming or plasma technology
- Component bonding (1C, boosted 1C, 2C)
- Thermal interface materials processing (gap filler, TIM; 1C, 2C)
- Screw connections (threaded or self-drilling)
- Spray sealing of weld seams and screw connections
- Sealing by waxing, spraying or direct application
- Battery housing sealing with cold and hot butyls up to 180 °C
- Spray application of floor module protection on battery tray/floor panel
Our one-stop shop service ensures that your production process implementation is fully optimized. Including:
- First-class expertise in battery production application systems and production process automation
- Complete production process design
- Application components tailored to your requirements
- A wide network of technology suppliers to meet process requirements
- End-to-end solutions from a single source
Our expertise in concept engineering, application systems and plant automation covers all the process flows required to implement your battery cell or module production process, including assembly and mounting. Get in touch – we’ll be happy to provide you with comprehensive advice on our end-to-end solutions.
Our systems enable virtually any application process with, in some cases still emerging, technological demands. Our cutting-edge technology centre, where we carry out the required material and component tests, also plays a key role.
A selection of our partners and customers in Electromobility:
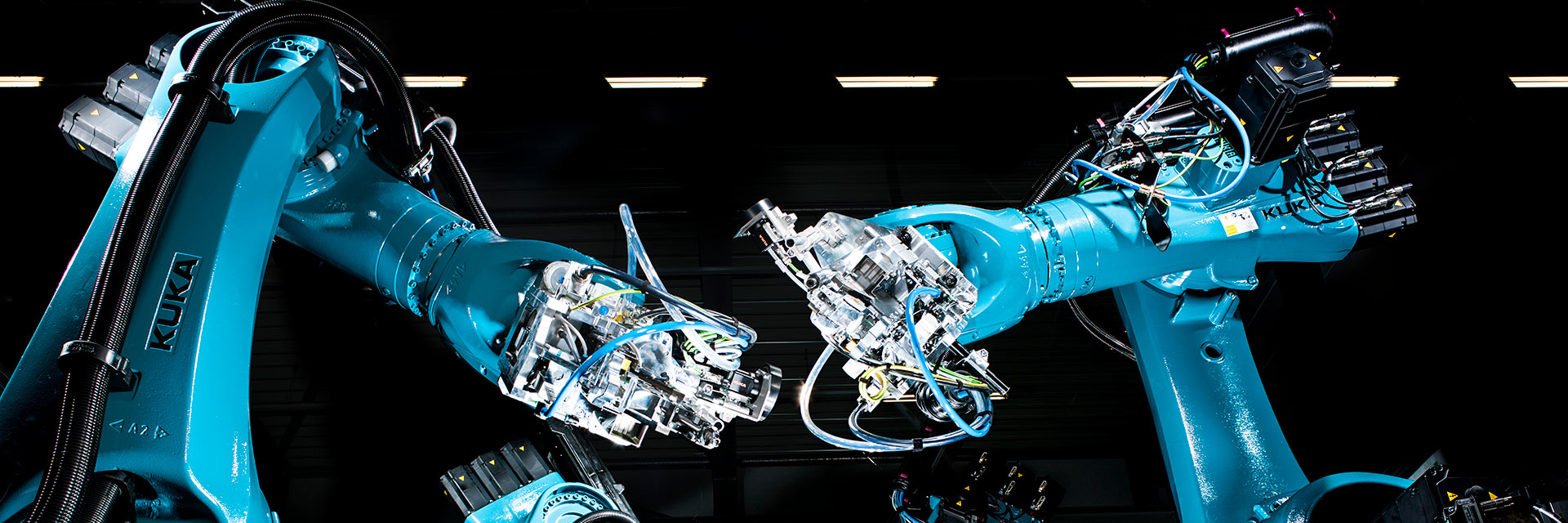