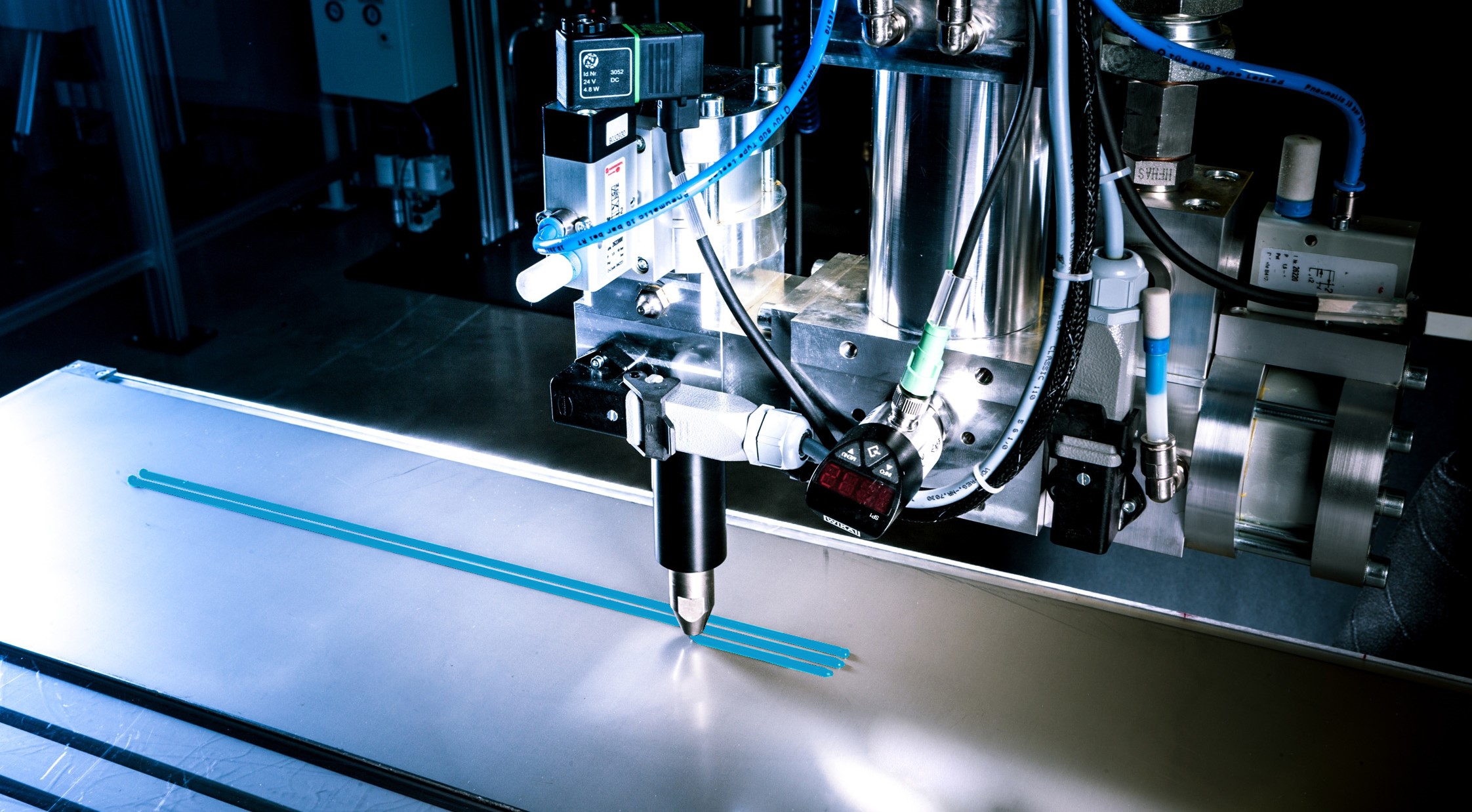
Thermal conductive pastes as an essential component of batteries
The battery modules generate heat during the energy output for the drive which needs to be dissipated as best as possible. That's why so-called gap fillers (also known as thermal interface material, or TIM for short) are used in the manufcaturing of electric batteries. These gap fillers posses heat-conducting properties in order to dissipate the heat which is generated during the operation in the most beneficial way and thus to ensure increased safety and service life.
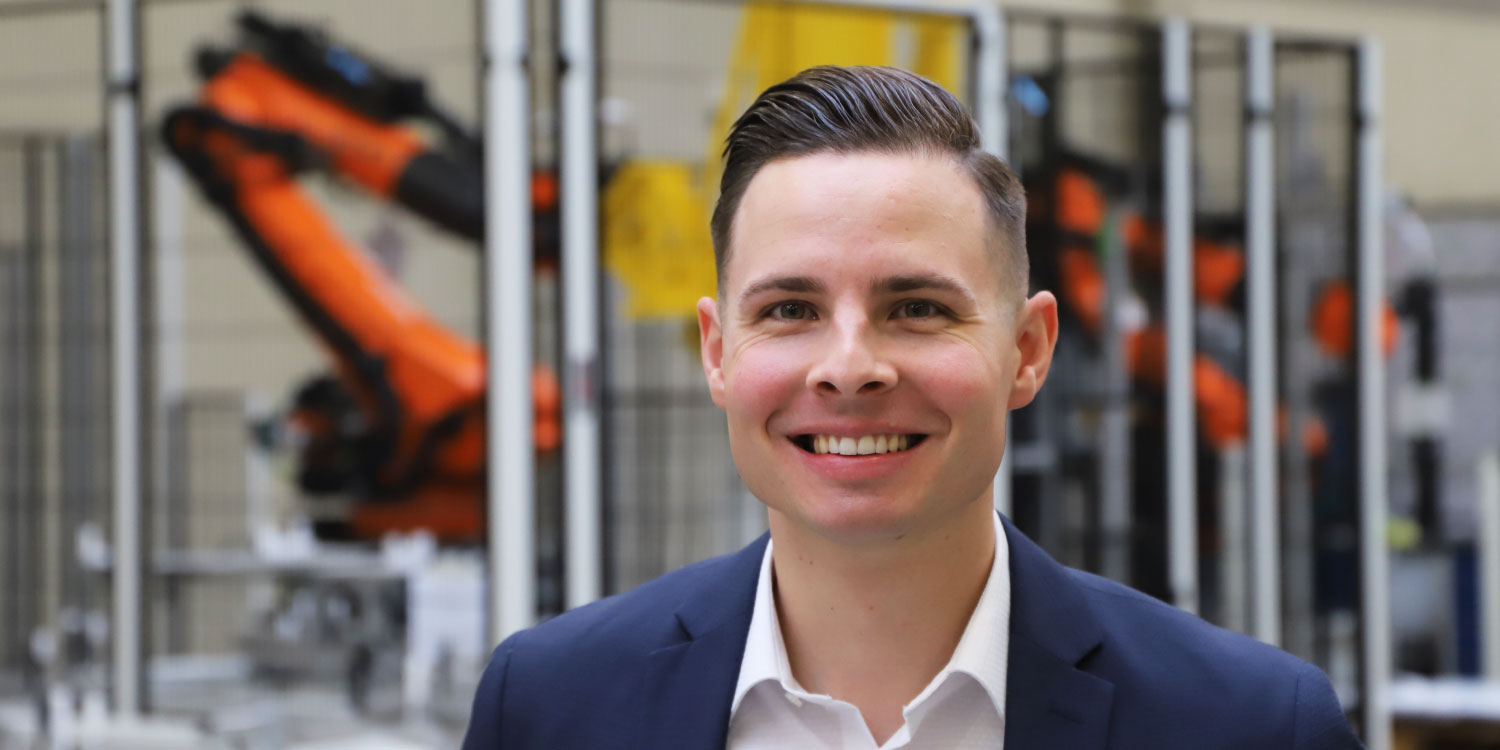
Characteristics of the thermal conductive pastes (gap filler)
Temperature management plays a major role in the production of battery packs. Batteries may only be operated within a certain temperature range to protect them from overheating during the charging and discharging process.
Thermal conductive pastes and gap fillers have high thermal conductive properties. Different surface conditions and tolerances of installed components cause air gaps. Since air has a very low thermal conductivity, it is very challenging to dissipate the generated heat. The application of gap fillers is aimed at eliminating the air gaps and improving the dissipation of the heat generated.
The service life span and safety of certain products in the electric battery production and consumer electronics increases significantly through the optimization of heat management and heat dissipation.
Application technology for the application of thermal conductive pastes
Application of gapfillers
The exact composition of gapfillers matches with thermal conductivity of the thermal contact in the application. Most gapfillers consist of silicones and are applied as liquid into cavities or paste form as a 1C oder 2C application to the corresponding component. A precise application without air inclusions is essential to ensure the full thermal conductivity of the thermally conduct pastes.
Applying thermally conductive pastes is a challenging aspect because they must be applied in a high volume and are usally highly abrasive which causes the technology to wear out quickly. However, ATN has developed stable application technology for the application of gap fillers.
Low costs through efficient processing
The high-class components in ATN's application technology are used when applying gap fillers. Thermally conductive pastes are high in weight and are very cost-intensive. ATN's products have a high precision, durability and efficiency. Therefeore, they are suited optimally for application of thermally conductive pastes. ATN's in house application control system IFC adjusts and monitors quantities of the material seamlessly even during the application process of the gap fillers. ATN provides you with application technology specially adapted to the chemical properties of the heat conductive pastes.
Take a look at our Flyer Gap Filler for more information!
Reliable application technology for battery manufacturing
As an end-to-end solution provider for battery production, our wide range of application systems can be implemented in high-quality filling and sealing applications that meet your materials requirements.
A new and efficient way of transporting heat to to external surfaces is to fill the finished cavity of an electrical component or battery module with a liquid 2-component gap filler. The mixed material is introduced into the component in this process. The cavities are completely filled due to the good flow properties of the gap filler. Pressure monitoring ensures the maximum filling of the component.
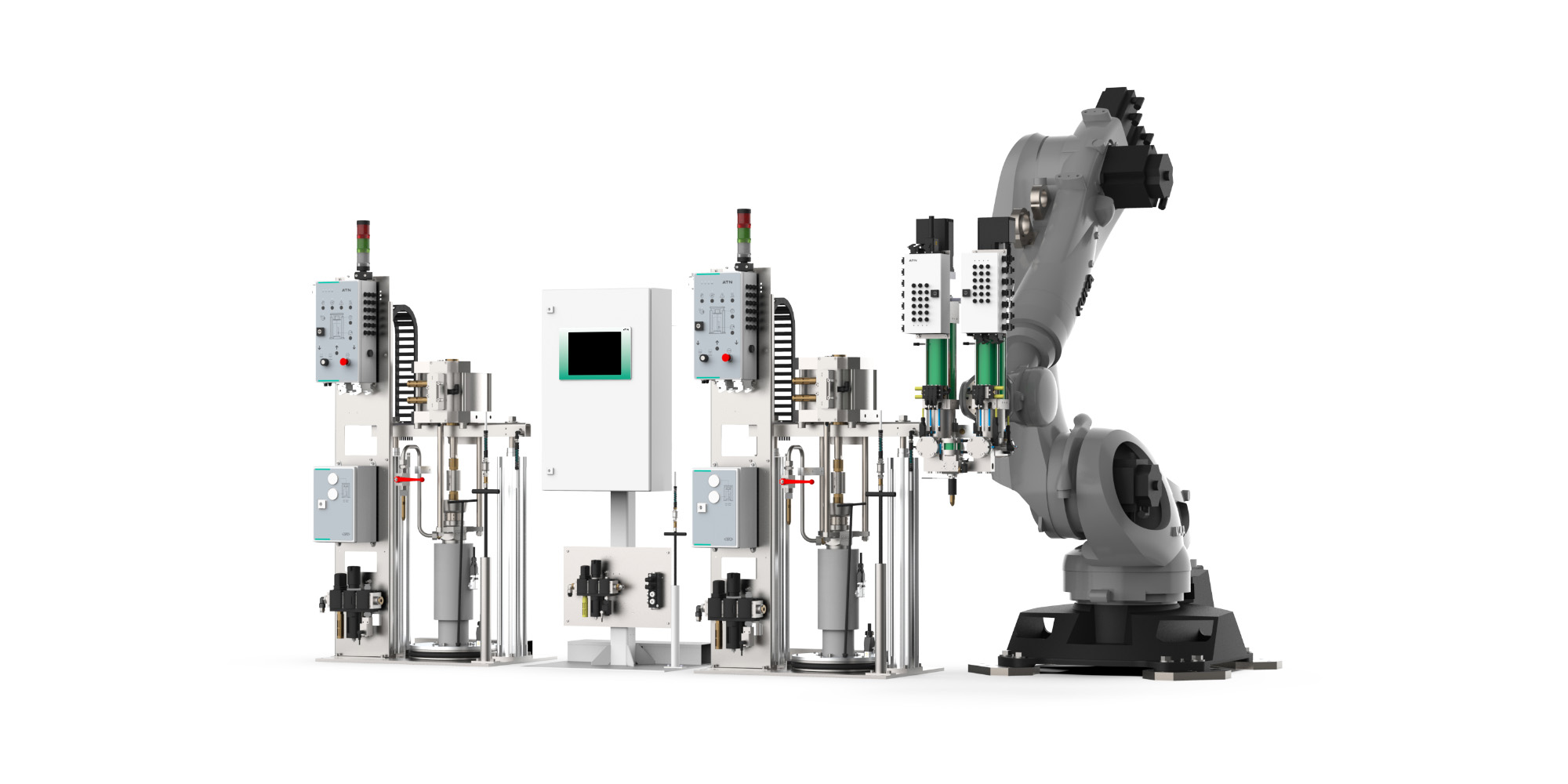
The special challenges of heat-conducting pastes place high demands on the material supply. ATN's drum emptying systems make it possible to convey gap fillers from 20 - 1,000 liter containers. The cost-intensive material can be conveyed almost completely out of the drums using a residue-optimized follower plate in order to increase efficiency and reduce material costs.
A double drum system can also be used to ensure seamless conveying of the material during a drum change.
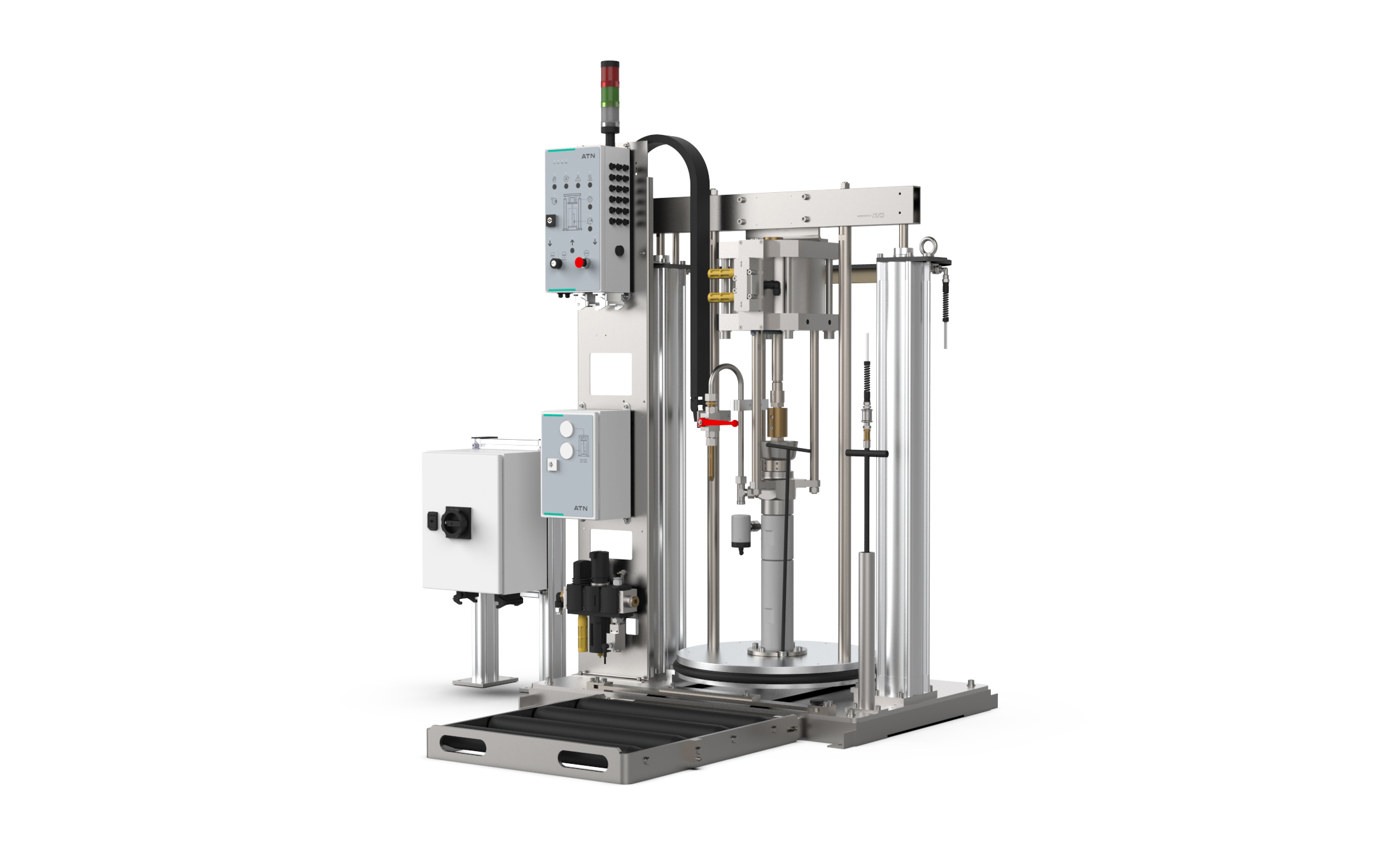
Material hoses are an important part of the material conveying chain. The material hoses from ATN are characterized by their special flexibility, high quality and chemical resistance to the heat-conducting pastes. Additional heating for processing gap fillers is possible with the material hoses.
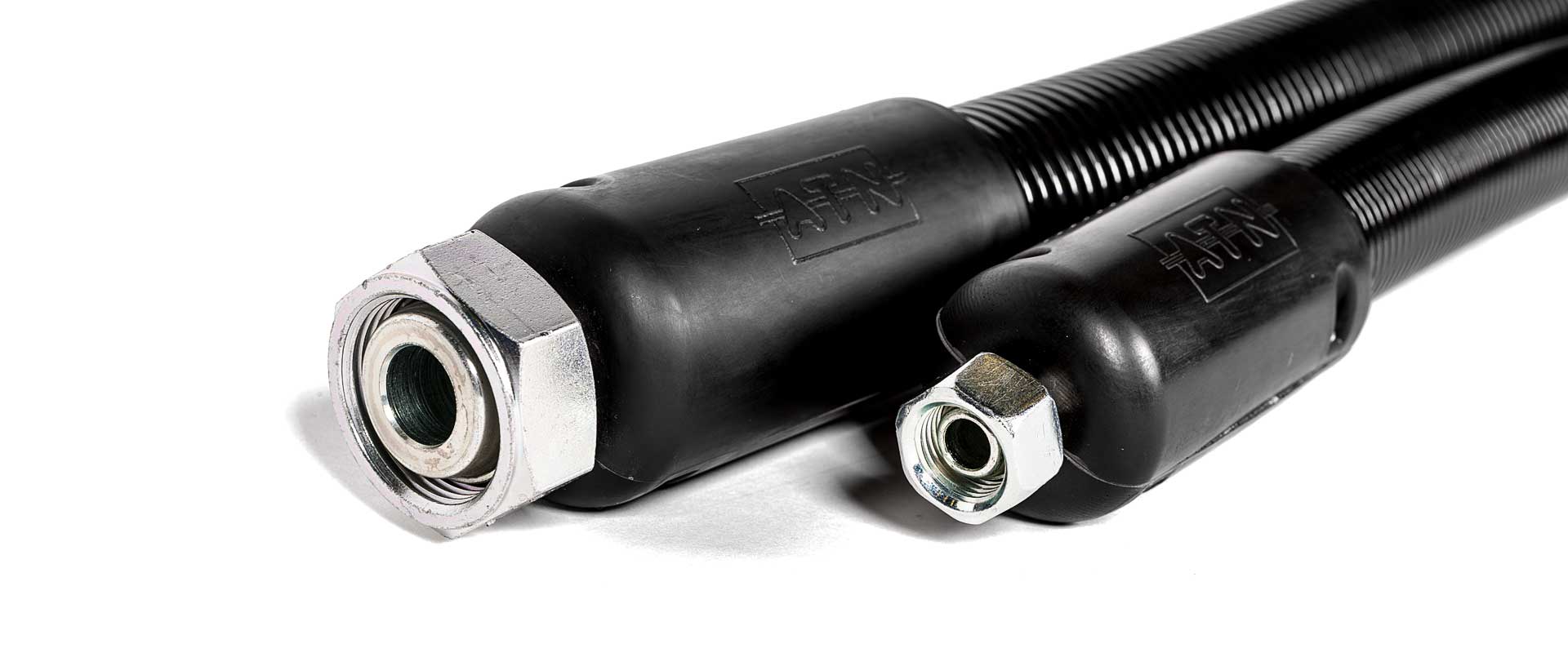
At the heart of the material application process are the electro-volume dispensers, which are available for different dispensing and application quantities. The electro volumetric dispensers guarantee and ensure precise application with a repeat accuracy of over 99 %. This means that ATN dispensers can also be used to realize potential efficiency and cost savings in material processing.
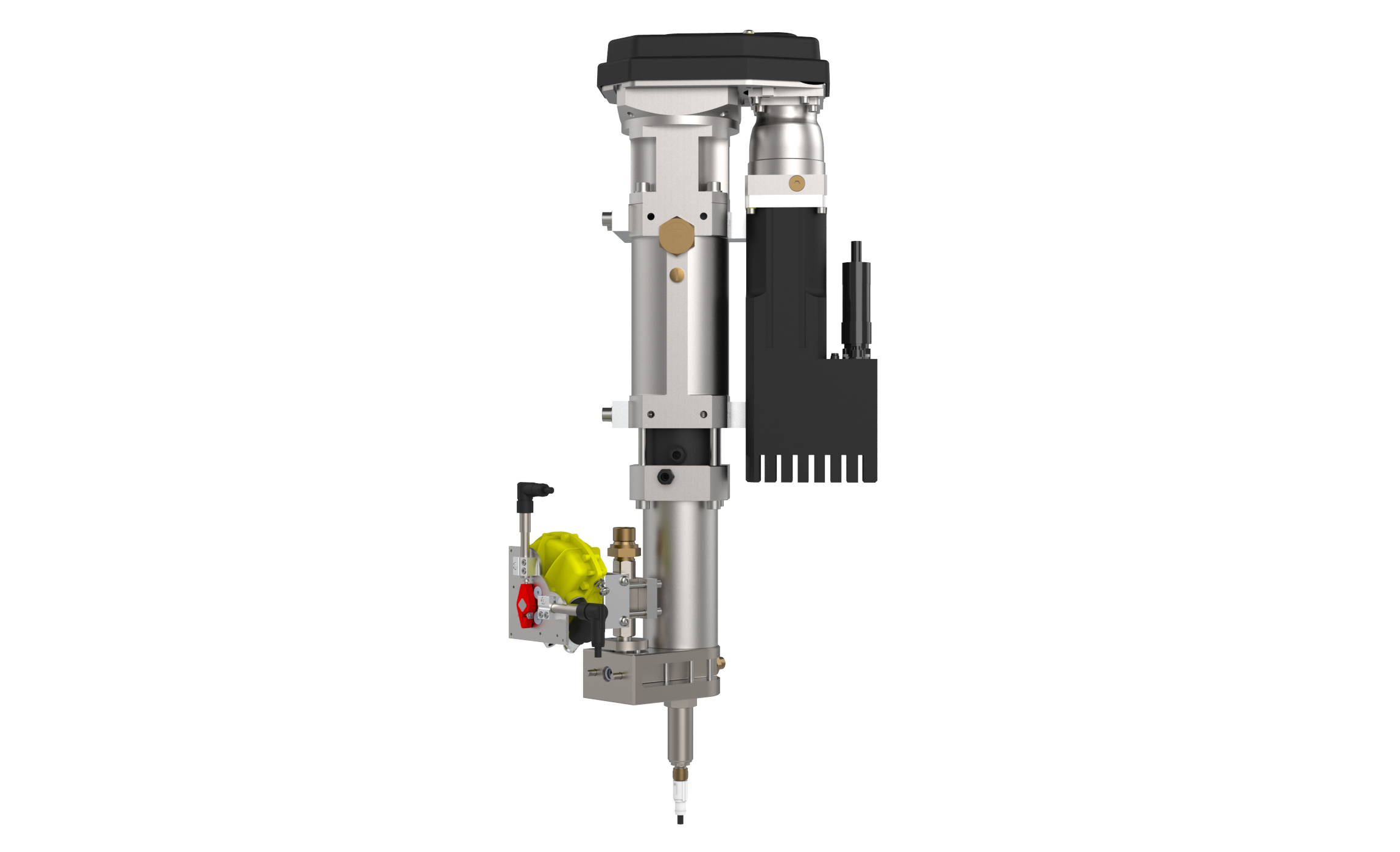
The range of ATN applicators as the last component in the chain of application of heat-conducting pastes is wide. The use of 2-component application systems means that almost any possible material composition can be applied. This means that the bead diameter can also be adapted to the specific use of the thermal pastes.
ATN's VN8 and VN14 applicators are used for this purpose.
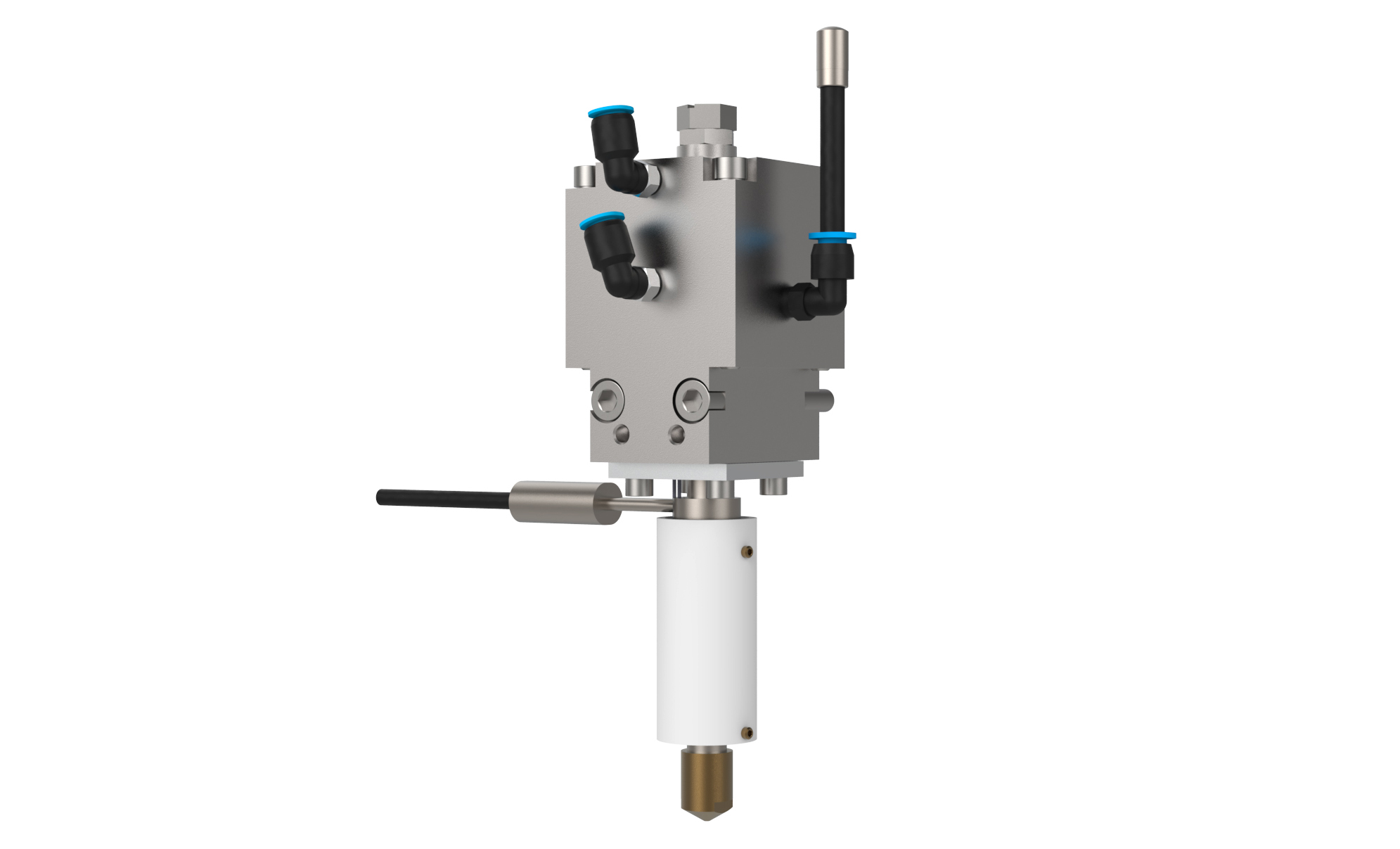