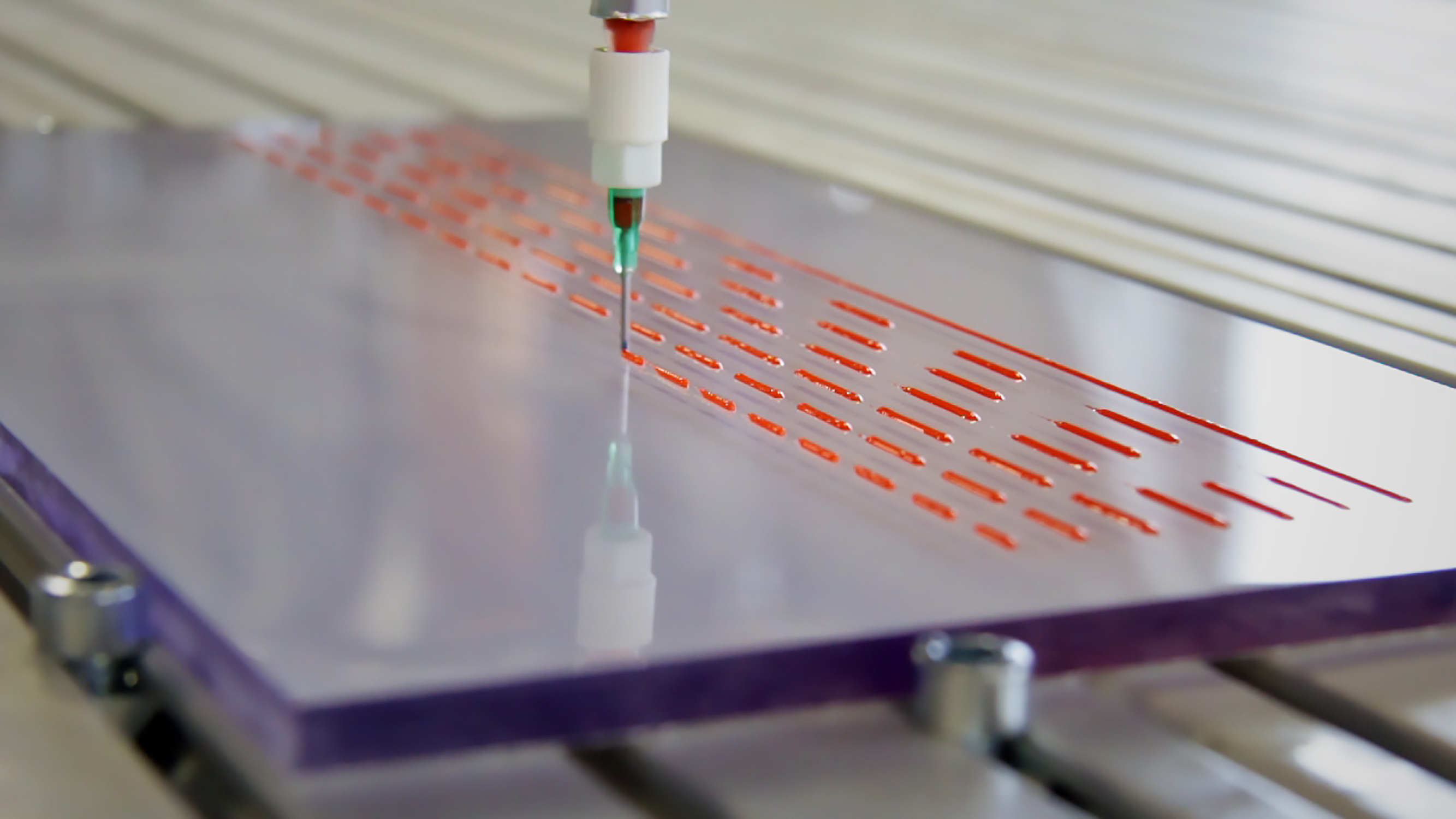
"Graduated bonding" - process innovation in adhesive bonding technology
In cooperation with the IPF (Leibniz Institute for Polymer Research Dresden e.V.), ATN has developed a patented and novel process called "graduated bonding", which increases the load capacity of structural bonded joints by up to 50 %. The improved load capacity of bonded joints opens up to profound new applications in various industries. These include expanding freedom of designs and manufacturing as well as material savings in the use of adhesives and substrate materials.
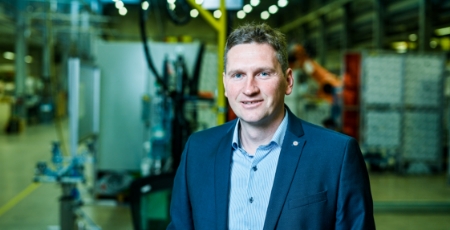
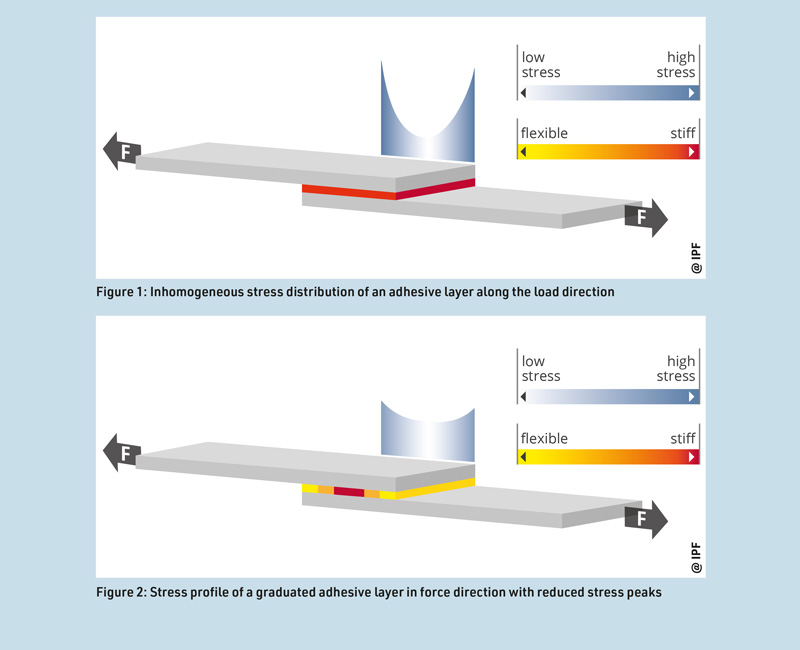
The initial situation for graduated bonding
Structural bonded joints exhibit a variable stress profile within the adhesive layer when they are subjected to tensile loads, especially on long overlapping ends (lap length). The ends of the two bonded workpieces constitute the greatest stress on an adhesive layer and when overloaded, causes a failure of the bonded joint. Increasing the lap length would only make a small contribution to increase the load-bearing capacity.
How does graduated bonding work?
Implementation and application of a graduated adhesive layer
ATN and IPF have developed graduated bonding, a process that increases the load-bearing capacity of structural bonded joints. By changing the mixing ratios in an adhesive joint, the flexibility of the adhesive mixture is being influenced. This reduces stress peaks within the bonded joint and is achieving better load optimization of structural bonded joints. Thus, the bonded joint can transmit significantly higher loads.
Different mixing ratios can be realized by a 2-component application. ATN's application technology is able to realize this kind of application. With the help of ATN's EVD dosing units, the corresponding variable adhesive mixture is achieved by means of an adaptive control technology and the customized mixed adhesive compounds are applied to the workpiece and a graduated adhesive joint is created. The material for the adhesive joint is being applied by using an automated application process.
The results are explicit
The test results of the research show that graduated adhesive layers have a significantly optimized adhesive bond compared to a standard bond. With a long lap length, the breaking force can be increased by up to 50 %. This means that the longer lap length can be subjected to greater loads or the area of bonded joints can be reduced while maintaining the same load. The advantages for bonding application and for future applications of adhesive bonding technology are manifold.
Become a partner and further develop adhesive bonding technology!
High development potential for graduated bonding!
To further advance graduated bonding and to implement it successfully in the industry, more exemplarity cases and bold decisions are needed. Reach out and conservate with our technical experts seated in our knowledge hub and learn more about the new graduated bonding process.
With this exchange of knowledge between experts, synergies and solutions may evolve which may benefit both sides! We are looking forward to your engagement and feedback!
Polymers are considered the basis of modern technologies and the starting point for innovative developments. Without the use of polymers, many of today's solutions in material and energy-saving lightweight construction, information technologies and medical therapies would be inconceivable. The IPF sees its task in the most diverse research projects in polymer technology in order to deepen and expand the existing knowledge and understanding.
Through knowledge and application-oriented research, solutions for social and technologically relevant questions are developed. The cooperation of natural and engineering scientists conduct exvellent basic research, whis is supported by industrial cooperation through the IPF so that innovations find their ay into the various industrial applications. Learn more about the IPF here:
We as ATN are proud to cooperate with the IPF as a renowned and strong partner for innovations and furher developments!
Classic joining methods such as welding, or rivetating being increasingly replaced by the bonding of materials or combined with the positive properties of adhesive bonding. Since its establishment, ATN has been supplying application and automation systems for adhesive bonding technology. However, the knowledge and know-how built up is also used for further continous development and improvement of the status quo together with academic partners or the end customers.
Various processes for the bonding of workpieces, their pretreatment, cavity foaming, sealing and gasketing are part of ATN's product and process portfolio. With "graduate bonding", ATN and IPF have once againg succeeded in further developing adhesive bonding technology and opening new techniques and processes.