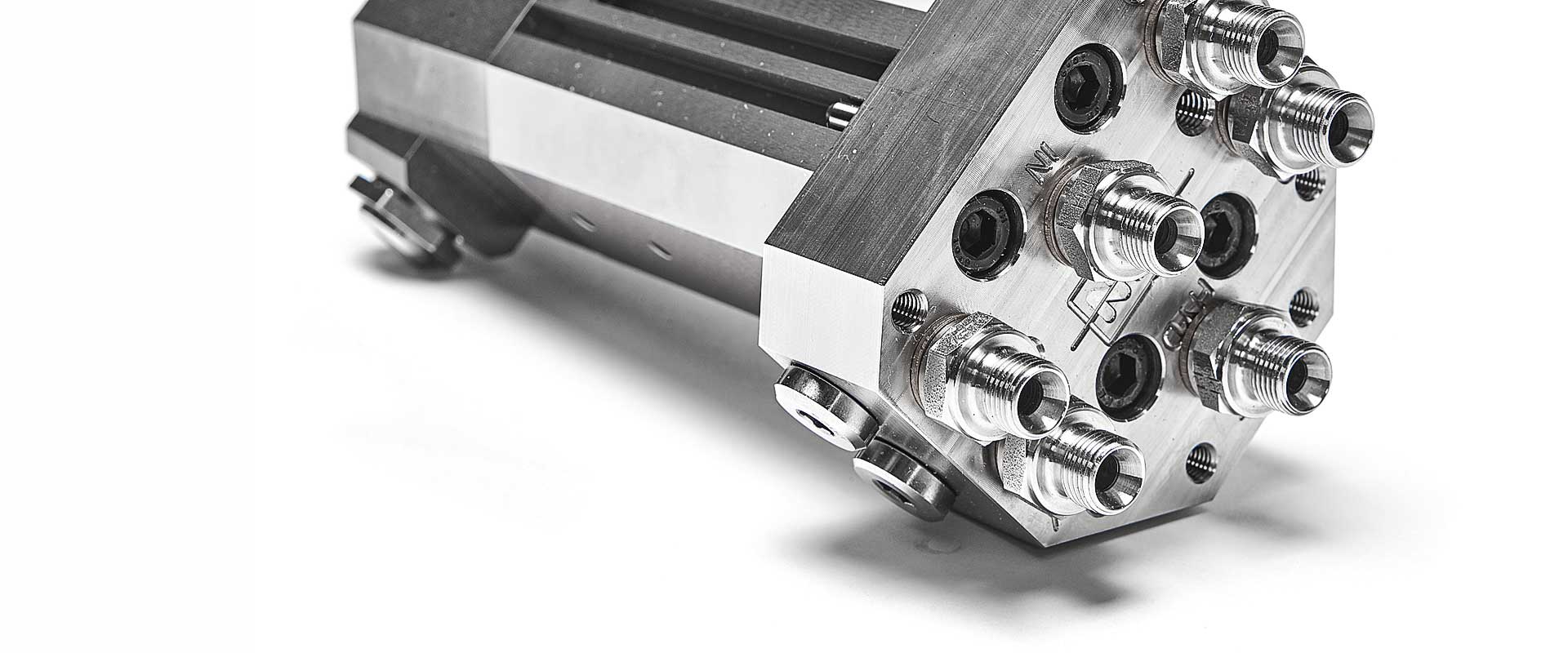
CAVITY FOAMING - RIM (REACTION INJECTION MOULDING)
Reaction Injection Moulding (RIM) is a primary forming process in which two components are mixed together and injected into a mould or cavity. The process is used to manufacture products such as moulded plastic parts and soft and hard foams.
We've acquired extensive experience and process knowledge in Reaction Injection Moulding technology based on ATN RIM systems used in the automotive industry.
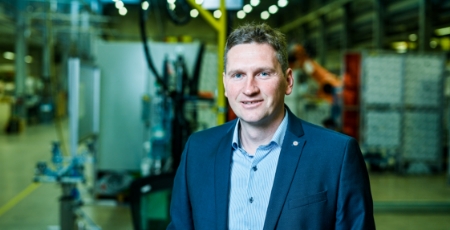
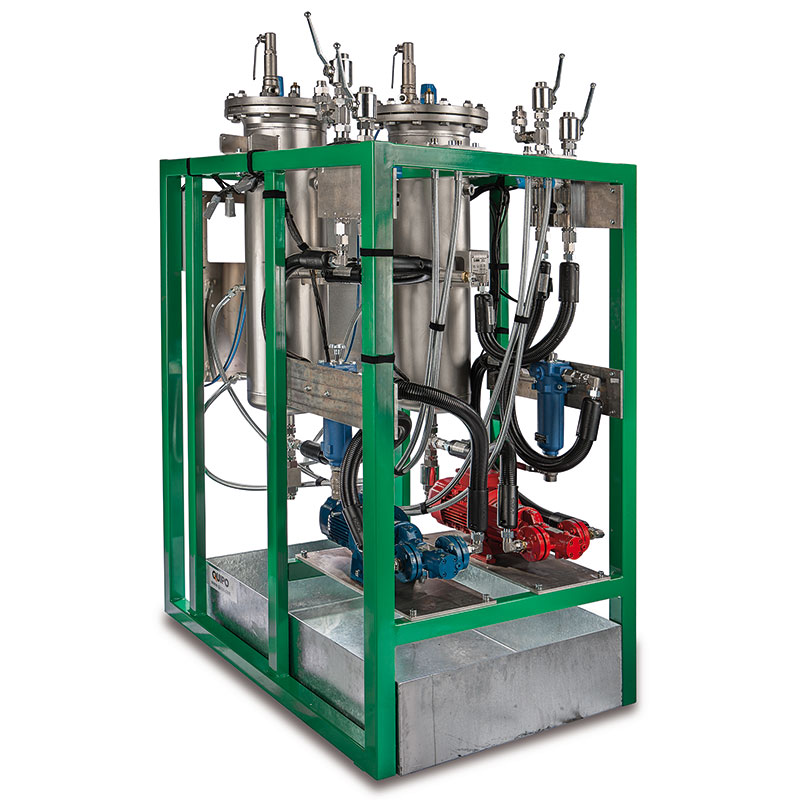
ATN Reaction Injection Moulding application system for foaming
ATN’s RIM system is specially designed for foaming applications such as injecting insulating foam in body cavities. It enables precision dispensing and reliable processing of the raw materials.
Our experts design the corresponding feed and dosing systems and select the correct application pressure based on the flow rate and viscosity of your material.
The function principle of a RIM system
Reaction injection moulding (RIM) is used to fill cavities with a reactive mixture. The chemical reaction (‘R’) takes place immediately after mixing in the applicator’s mixing chamber. The applicator then injects (‘I’) the mixed material into the cavity. The reaction continues in the cavity, or mould (‘M’), and the reactive mixture – the 2C PUR foam – cures. ATN’s Reaction Injection Moulding system is specially designed for processing polyurethane foam. This is made from polyol and isocyanate in a polyaddition reaction where the two components form an isotropic material or a foam.
When water is added, the reaction produces CO2, which influences the density of the foam.
RIM system applications
The RIM process is used in many industries and the technology is suitable for a wide range of applications. Depending on the composition of the PUR components, it can produce solid moulded plastic parts such as panels, bumpers and steering wheels.
When used for polyurethane foam production, RIM technology is suitable for quite different applications. In the automotive industry for example, vehicle seats are made from PU foam, and RIM systems are used to foam-fill body cavities to improve noise insulation.
The technology is increasingly popular in the construction industry, where mobile RIM systems are used to inject PUR insulation foam into buildings.
Design and function of ATN RIM systems
The technology in our RIM systems is based on ATN’s in-house two-component dosing systems in conjunction with components specially developed for the RIM process. The controller is designed to your in-house standards.
Key components in the direct application process are the PU supply system for the foam, plus the electronic volumetric dosing systems and the foam applicator for high-precision material dosing and application. A recirculation system keeps the material moving at the right conditions for application to ensure its constant availability.
Our experts design your foaming systems and their components based on your requirements. Find out more about ATN RIM technology and request your customized system concept now.
End-to-end application and automation solutions
Looking for an end-to-end solution for your special-purpose machine or system? Get in touch – we’ll be happy to provide you with comprehensive advice on all aspects of application, assembly and automation solutions. We will fully implement your entire process, from conceptual design to on-site commissioning. We offer industry solutions for the automotive, household appliances, aerospace, electronics, renewable energies, chemical, construction and furniture industries as well as medical technology and pharma life science.
Implement your application process with ATN
ATN’s reliable application systems comprise all the components you need for application across all orders. They include barrel emptying systems, dosing systems, application towers and nozzle cleaning systems as well as many accessories. ATN is your partner for reliable precision fluid dosing systems. ATN application systems guarantee a consistent quality of your processes.